operate a small biomass pellet mill
Flat die biomass pellet mill belongs to small scale pellet mill. It is very popular in customers because of its high quality, easy operation and long service timeFlat Die Biomass Pellet Mill Working Principle
Flat die pellet mill can be further divided into D-type pellet mill and R-type pellet mill. The working principle between D-type pellet mill and R-type pellet mill is a little bit different, you can check here to see their difference in detail.
In D-type pellet mills, the flat die is driven by the main shaft to rotate, and the fixed roller would turn vertically driven by the flat die in the mean time. It is opposite to the R-type pellet mills. In R-type pellet mills, the roller rotates actively while the flat die stays stationary.
Flat die pellet mills use a flat die with many holes. When the biomass materials were introduced to the pelletizing chamber and fell on the die, the roller or the die would start rotating, and the materials would be pressed into the holes in the die and formed into slender pillars, and a knife on the other side of the die would cut them into small pellets.
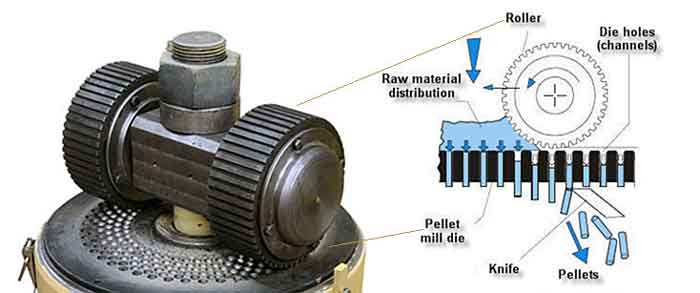
How to operate a Small Pellet Mill Correctly
1. Biomass raw material requirement
Raw biomass materials fed into the pellet mills should meet the moisture content requirement of 8-18%. Materials failed to meet this requirement will not only seriously affect the biomass pellets quality but also damage the pellet mill.
2. Grinding process for new flat dies
The new flat die need to be grinded first before it is putted into use. The detailed grinding procedure is:
1) Mix 5kg raw material powder, 1kg fine sand, and 1kg waste engine oil together.
2) Activate the biomass pellet mill, feed the mixed material into it and adjust the roller bolt into proper position.
3) Keep the pellet mill working for an hour. If the biomass pellet mill didn’t function well, the operator should loose the roller bolt slightly until the pellet mill can make pellets normally. If the small biomass pellet mill still have functioning problem, the operator should clear the die holes, and run the grinding process again.
When a day’s work is finished, the operator should use the mixture of raw material and 10% waste engine oil to fill the flat die holes, so that the pellet mill can be used directly next time.
3. Adjustment of the clearance between roller and die
The clearance between the roller and the flat die in a small pellet mill influences can have a large impact on the pellets quality. The clearance between the roller and the die is required to be 0.05-0.3mm. If the clearance exceeds this range, the material layer will be too thick to be evenly distributed, and the pellet productivity will be decreased. If the clearance is not enough to reach this range, the roller and the die will be severely worn.
4. Choose proper compression ratio (the ratio of die thickness and die hole diameter)
The compression ratio and the pellet mill productivity is inversely proportional. The small compression ratio will lead to a high output rate, but the pellets produced will have low hardness and be easy to break. The high compression ratio will lead to low productivity but the pellets will have a high density. The key is to choose according to the raw materials you would use.
5. The adjustment of pellet length
The pellets length can be adjusted by adjusting the pellet cutter length in the outlet of the pellet mill.
GEMCO is a leading small pellet mill manufacturer in China. We provide a series high quality pellet mill for farm or home use.
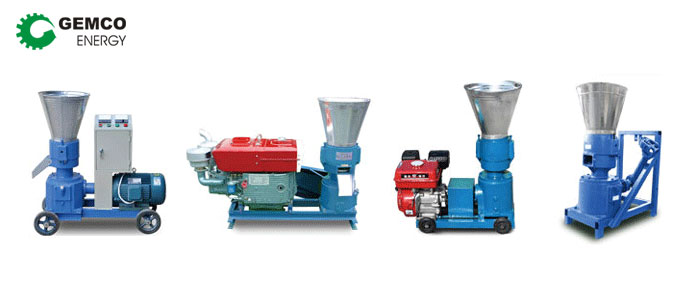
Get In Touch